In the dynamic world of cosmetics and personal care, precision and efficiency are key to delivering high-quality products. At the heart of every successful lotion, cream, or gel production line lies a reliable filling system. Whether you’re scaling up a boutique brand or optimizing a large-scale manufacturing facility, understanding the ins and outs of lotion filling lines is essential. Granda, your trusted partner in daily chemical machinery, is here to guide you through the fundamentals of building, using, and maintaining a top-tier filling system that meets your production needs.
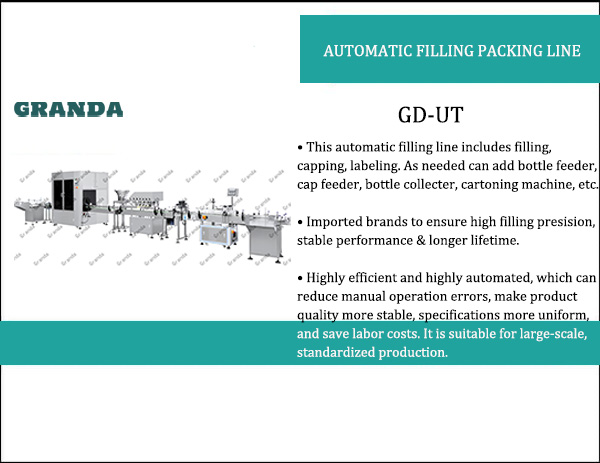
Table of Contents
- What Is a Lotion Filling Line?
- Core Components of a Lotion Filling System
- Choosing the Right Filling Line for Your Needs
- Installation & Commissioning
- Operation Best Practices
- Maintenance & Troubleshooting
- Granda’s Custom Solutions for Your Production Goals
What Is a Lotion Filling Line?
A lotion filling line is an integrated system designed to accurately dose, dispense, and package liquid to semi-solid products like lotions, creams, serums, and gels into various containers—from small tubes and bottles to large jars and pump dispensers. Unlike basic manual fillers, modern automated lines streamline the process, ensuring consistency in fill volume, reducing waste, and enhancing production speed. These systems are critical for maintaining product quality while meeting the demands of regulatory compliance and consumer expectations.
Core Components of a Lotion Filling System
A typical lotion filling line comprises several key components, each playing a vital role in the production process:
1. Filling Machine
The centerpiece of the system, available in various types:
- Piston Fillers: Ideal for viscous products like thick lotions and creams, using piston-driven mechanisms for precise volume control.
- Peristaltic Pump Fillers: Gentle on shear-sensitive formulations (e.g., serums with active ingredients), using flexible tubing to prevent product degradation.
- Gravity Flow Fillers: Suited for low-viscosity liquids, relying on gravity for simple, cost-effective dispensing.
2. Conveyor System
Transports containers through the line, ensuring seamless alignment with the filler. Features include adjustable speed controls, anti-slip belts, and automatic bottle positioning for accuracy.
3. Capping & Sealing Units
After filling, containers are capped or sealed with precision:
- Screw cappers for pump bottles
- Induction sealers to create airtight lids, preventing contamination and leakage.
4. Control Panel & Automation
Modern lines feature PLC (Programmable Logic Controller) systems that allow operators to set fill volumes, adjust speeds, and monitor performance in real time. Touchscreen interfaces simplify programming and troubleshooting.
5. Product Hopper & Feed System
Holds the bulk product and feeds it into the filler, often equipped with agitators to maintain consistency in thick formulations and prevent sedimentation.
6. Quality Control Sensors
Optical or weight sensors check for under-filled or over-filled containers, ensuring every product meets your specifications before moving to labeling or packaging.
Choosing the Right Filling Line for Your Needs
Selecting the optimal system depends on several factors:
1. Product Characteristics
- Viscosity: Thin lotions (e.g., body lotions) vs. thick creams (e.g., anti-aging formulas) require different pump types (peristaltic vs. piston).
- Fill Volume: Small batches (10-100 mL) vs. large containers (1-5 L) dictate nozzle size and filling speed.
- Sensitivity: Shear-sensitive products need gentle handling to preserve texture and active ingredients.
2. Production Scale
- Boutique/Medium Scale: Semi-automatic lines offer flexibility for small runs and frequent product changes.
- High Volume: Fully automated systems with integrated conveyor belts and robotic capping maximize output (up to 200+ bottles per minute).
3. Container Type
Whether you use HDPE bottles, glass jars, airless pumps, or flexible tubes, ensure the filling line’s grippers, nozzles, and capping mechanisms are compatible.
4. Regulatory Compliance
Look for systems made from FDA-approved materials (stainless steel 316, food-grade polymers) and designed to meet GMP standards for easy cleaning and sanitization.
Installation & Commissioning
- Site Preparation: Ensure a clean, level floor with proper electrical and air supply (for pneumatic systems).
- Professional Setup: Partner with Granda’s expert technicians to assemble and align components, calibrating the system for your specific containers and products.
- Testing: Run trial batches to verify fill accuracy, capping torque, and conveyor speed. Adjust parameters until perfect consistency is achieved.
Operation Best Practices
- Training: Ensure operators understand the control panel, safety protocols, and quick-release mechanisms for nozzle changes.
- Maintenance Schedule: Follow daily checks (lubrication of moving parts, filter cleaning) and weekly inspections (belt tension, sensor alignment).
- Product Changeovers: Use quick-disconnect nozzles and easy-to-clean hoppers to minimize downtime when switching between formulations.
Maintenance & Troubleshooting
Routine Maintenance
- Cleaning: Disassemble and sanitize contact parts (nozzles, hoppers) daily to prevent product buildup and bacterial growth.
- Lubrication: Apply food-grade lubricants to conveyor chains and piston rods to ensure smooth operation.
- Calibration: Regularly check fill volume accuracy using weight scales and adjust pump strokes or nozzle dwell time as needed.
Common Issues & Solutions
Problem | Possible Cause | Solution |
---|---|---|
Inconsistent Fill Volume | Clogged nozzle, worn piston seals | Clean nozzles, replace seals, recalibrate |
Leakage at Nozzle | Misaligned nozzle tip, damaged O-rings | Realign nozzle, replace O-rings |
Container Misalignment | Conveyor belt misadjustment, faulty sensor | Adjust belt tension, recalibrate sensors |
Air Bubbles in Filled Product | Agitator not engaged, fast filling speed | Activate agitator, reduce filling pressure |
Granda’s Custom Solutions for Your Production Goals
At Granda, we understand that no two production needs are the same. That’s why we specialize in turnkey lotion filling lines tailored to your product, scale, and budget. Our solutions include:
- Modular Systems: Add capping, labeling, or cartoning units as your business grows.
- Sanitary Design: Easy-to-clean surfaces and corrosion-resistant materials for pharmaceutical-grade hygiene.
- Energy Efficiency: Low-power motors and smart controls to reduce operational costs.
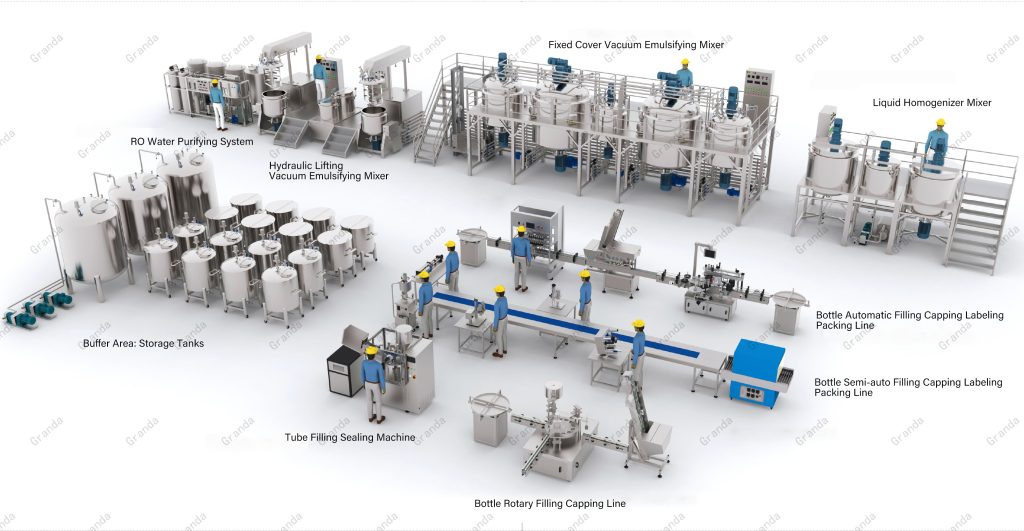
Whether you’re launching a new lotion line or upgrading an existing facility, Granda’s team of engineers and technicians will work with you to design a system that prioritizes precision, reliability, and scalability.
Conclusion
A well-designed lotion filling line is the backbone of any successful personal care production facility. By understanding the components, choosing the right system, and maintaining it properly, you can ensure consistent quality, minimize waste, and meet market demands efficiently. Trust Granda to deliver innovative, custom solutions that empower your production goals—because your success is our priority.
Ready to build your ideal lotion filling line? Contact Granda today to discuss your project and request a free consultation.