As a core packaging equipment in daily chemical, pharmaceutical, food and other industries, the selection of tube filling and sealing machines directly affects production efficiency and cost control. This article analyzes the applicable scenarios of four mainstream machine types from three dimensions: output scale, packaging material types, and product characteristics, helping you accurately match equipment needs.
1. Start-up Clients: Small Batch Trial Production and Multi-variety Adaptation (Output 8-15pcs/min)
Recommended Solutions: Semi-Automatic Vertical Filling Machine + Semi-Automatic Hose Sealing Machine / Single-Head Semi-Automatic Filling and Sealing Machine
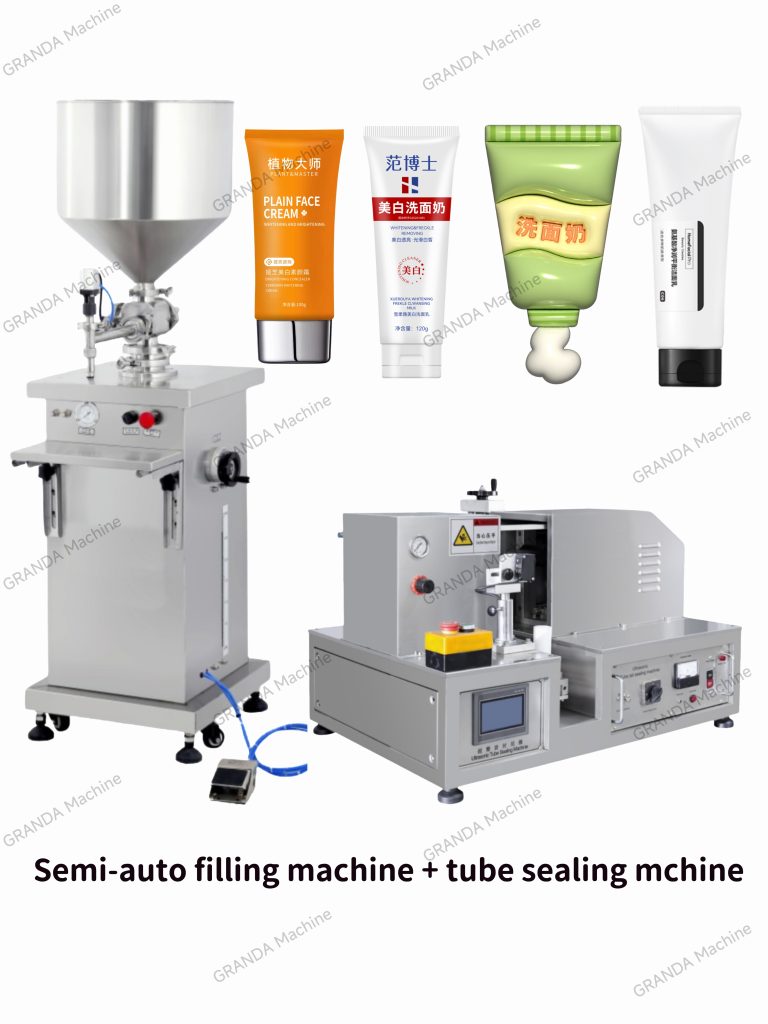
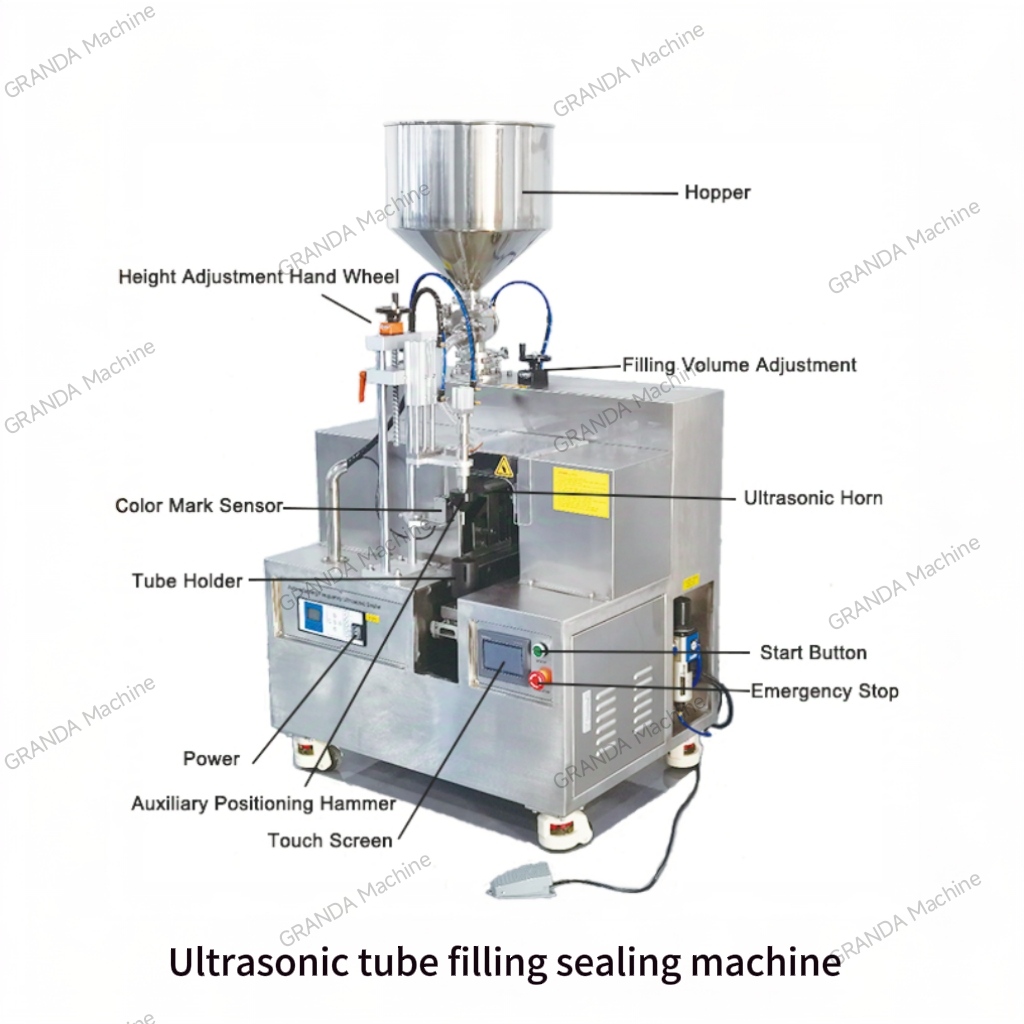
Application Scenarios
- Output Characteristics: Daily output < 4,000 pieces, suitable for new product R&D sampling, customized small orders, or seasonal product production
- Packaging Material Range: plastic tubes, composite tubes with a diameter of 10-30mm and a length of 50-150mm (manual tube loading/centering required)
- Product Characteristics: Pastes (such as face creams, ointments), semi-fluids (such as hair conditioners), materials with particles (anti-clogging pump heads can be selected)
Equipment Advantages
- Cost Control: Equipment investment is about $4,000-$6,000, only 1/5~1/3 of the fully automatic model
- Flexible Switching: 10-minute quick mold change, supporting the production of multi-specification hoses/tubes
- Low Operation Threshold: No professional technicians required, can be operated after 30 minutes of training (equipped with a visual operation screen)
Typical Case
A handmade soap brand initially used a single-head all-in-one machine to achieve monthly production of 3,000 essential oil tubes. By manually adjusting the filling volume (5-30ml), it met the production of multiple SKUs such as hand creams and massage creams, with no faults in 18 months of operation.
2. Growing Clients: Medium Capacity and Process Optimization (Output 15-25pcs/min)
Recommended Solution: Semi-Automatic Turntable Hose Filling and Sealing Machine
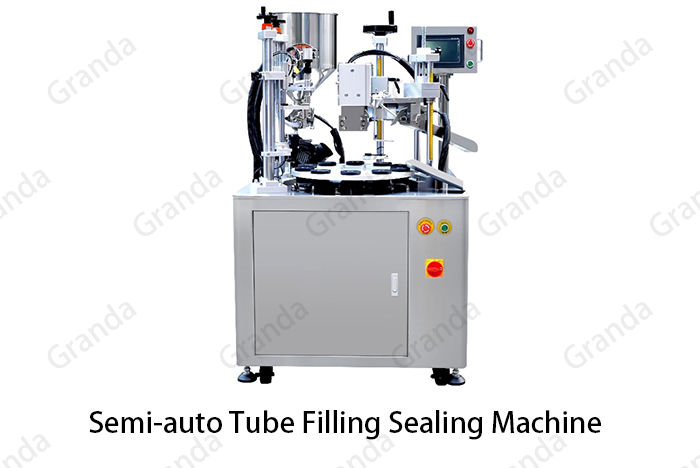
Application Scenarios
- Output Characteristics: Daily output 7,000 – 10,000 pieces, suitable for small and medium brands with various tube designs or low labour cost country.
- Upgraded Packaging Materials: Supports special-shaped tubes (elliptical tubes, beveled tubes), metal tubes (customized sealing molds required for aluminum tubes), with a diameter range expanded to 10-50mm (customized available)
- Production Requirements: Needs to integrate two processes of filling and sealing to reduce manual transfer loss (traditional semi-automatic requires manual tube transfer with a loss rate of about 3%, while the turntable type is reduced to 0.5%)
Equipment Highlights
- Efficiency Improvement: 6-station turntable design, 40% more efficient than single-head machines (stable operation at 20pcs/min)
- Sealing Quality: Standard constant temperature heat sealing system (temperature error ±2℃), aluminum tube sealing strength ≥8N/mm (in line with pharmaceutical packaging standards)
- Intelligent Detection: Functions such as automatic shutdown for missing tubes and abnormal filling volume alarm, reducing manual monitoring costs
Adaptation Case
A regional toothpaste factory used a turntable-type equipment to achieve mixed production of 3 specifications (75g/120g/200g) of toothpaste tubes. By replacing the filling nozzle (5-minute quick disassembly and assembly), it met the filling needs of pastes with different viscosities (fluoride toothpaste/whitening toothpaste), with an annual output increased to 1.5 million pieces.
3. Large-scale Production: Full-process Automation and Precision Control (Output 30-40pcs/min)
Recommended Solution: Fully Automatic Hose Filling and Sealing Machine (Linear/Servo-Driven)
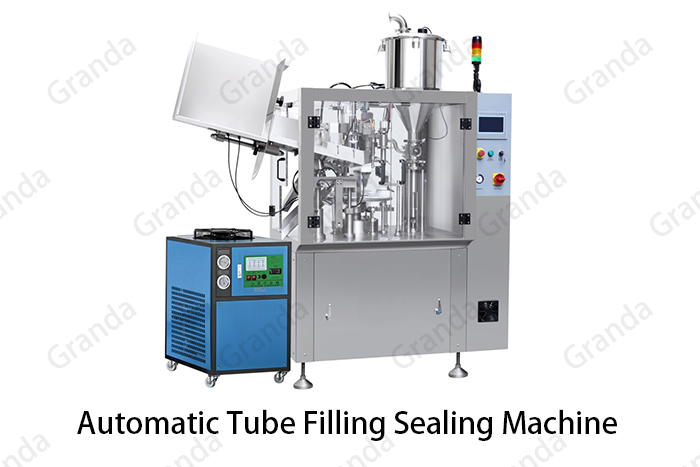
Application Scenarios
- Output Requirements: Daily output 10,000 – 20,000 pieces, suitable for large-scale production in the mature stage of the brand
- Packaging Material Compatibility: Supports the full range of hose materials (including high-barrier composite tubes), and can automatically load the tubes.
- Quality Standards: Needs to comply with GMP certification (equipment main body 304 stainless steel, food-contact parts with medical-grade polishing)
Technical Advantages
- Fully Automated Process: Automatic tube loading → positioning → filling → sealing → tail trimming → discharging, reducing 60% manual intervention (only 1 person for monitoring)
- Filling Precision: Servo motor-driven plunger pump, filling error ≤±0.5% (10ml filling volume error <0.05ml)
- Data Traceability: Standard production management system, which can record 12 parameters such as filling volume per batch, sealing temperature, and equipment operation time
Industry Application
A medical dressing enterprise selected a fully automatic model to achieve sterile filling of medical ointment tubes. The equipment integrates a CIP cleaning system (30-minute pipeline cleaning), meeting the strict cleaning verification requirements of the medical industry, with an annual output of 3 million pieces and a yield rate of 99.2%.
4. Ultra-high-speed Mass Production: Intelligent Production Line and Flexible Manufacturing (Output 100-120pcs/min)
Recommended Solution: High-speed Fully Automatic Filling and Sealing Production Line (Can Connect to Cartoning Machines, TPN Packaging Machines, etc.)
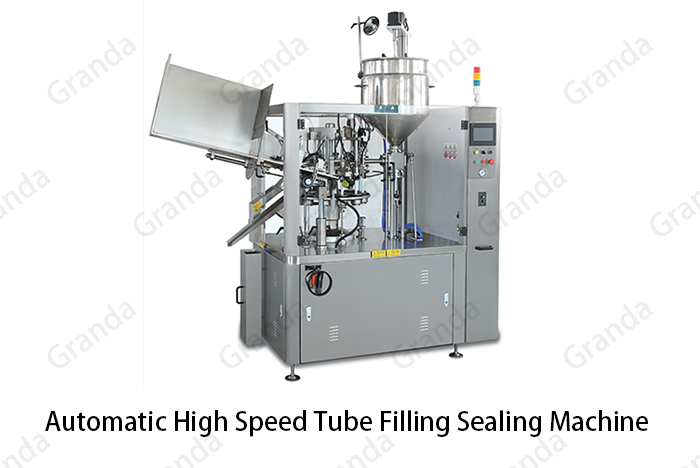
Application Scenarios
- Production Capacity Benchmark: Daily output >50,000 pieces, suitable for leading brand OEM factories and own production lines of daily chemical giants
- Production Line Configuration: Includes automatic tube sorting machine (processing speed 200pcs/min), filling and sealing main machine, visual inspection system (defect recognition rate 99.8%), cartoning machine, 3D dimension plastic film packaging machine
- Special Requirements: Supports hose surface printing registration (error <0.3mm), anti-counterfeit sealing (can customize laser coding + tear strip integrated function)
Core Value
- Efficiency Revolution: 1 high-speed line has a production capacity equivalent to 5 semi-automatic devices, reducing labor costs by 70% (only 2 people per double shift)
- Flexible Production: Model change time ≤25 minutes (mold quick-release structure + parameter memory function), supporting mixed production of multi-specification hoses
- Quality Closed-loop: Integrated metal detector (can detect metal impurities above 0.2mm²), online sealing strength detection (real-time rejection of unqualified products)
Benchmark Case
An international beauty group adopted a high-speed production line to achieve fully automatic production of 12 types of face cream tubes. By connecting MES system to ERP, it real-time monitors equipment OEE (comprehensive efficiency ≥85%), with an annual production capacity of a single line exceeding 50 million pieces, and unit production cost reduced by 22% compared with traditional production lines.
Selection Decision Four-factor Comparison Table
Selection Dimension | Start-up (8-15) | Growing (15-25) | Large-scale (30-40) | Ultra-high-speed (100-120) |
Initial Investment (Approx) | $4,000-$6,000 | $10,000 | $15,000 | $30,000 |
Labor Demand | 2 people/shift | 1 person/shift | 1 person monitoring | 2 people/double shift |
Packaging Material Switching Time | 10 minutes | 8 minutes | 5 minutes | 15 minutes (whole line) |
Quality Control | Manual Sampling | Automatic Detection | Full-process Traceability | Intelligent Quality Inspection Closed-loop |
Applicable Life Cycle | Trial Production/Small Orders | Stable Production | Large-scale Mass Production | Ultra-high-speed OEM |
Selection Suggestions
- Multi-variety and Small Batch: Give priority to semi-automatic equipment (single-head/turntable type), and reserve mold expansion interfaces (such as supporting 5-100ml filling range)
- Single Product Large-scale Production: Fully automatic models have higher cost performance (equipment cost can be recovered in 3 years), and pay attention to the material of the filling pump head (such as selecting corrosion-resistant materials for alcohol-containing products)
- Future Capacity Planning: It is recommended to choose upgradable configurations (such as adding an automatic tube loading module to the semi-automatic turntable type to upgrade to a fully automatic model)
- Compliance Requirements: Enterprises in the pharmaceutical/food industry need to confirm whether the equipment has passed CE/PED certification and supports CSV verification (computerized system verification)
Choosing the right filling and sealing equipment is essentially a balance between “current capacity requirements” and “future development space”. We provide free capacity evaluation and equipment selection plan design. Contact us to make an appointment for one-on-one consultation with a technical advisor to obtain a customized solution.
Guangzhou Granda Machinery CO., Ltd
www.grandamachinery.com